Inherit the wind
Rematec’s first International Forum on Wind Turbine Remanufacturing took place in Amsterdam. Adam Hill asked several experts to map out their thoughts for the nascent industry – and consider what lessons could be learned from the automotive sector.
There are hundreds of thousands of wind turbines operating worldwide – up to 350,000, according to one estimate. The first wind farms were built in the early 1980s and many of these have been replaced with new - larger - turbines over the last decade or so. Average turbine sizes are continuing to grow. According to the Global Wind Energy Association Global Wind Report 2018 the installed
capacity, combining both offshore and onshore wind, by last year was 591GW. In Europe, 22GW of that is slated to reach ‘end of life’ between now and 2023 and trade association WindEurope says: “A significant share of Europe’s wind turbine fleet will come to the end of its projected lifetime within the next 10-15 years.”
In Europe, 22GW of that is slated to reach ‘end of life’ between now and 2023 and trade association WindEurope says: “A significant share of Europe’s wind turbine fleet will come to the end of its projected lifetime within the next 10-15 years.”
In order to fulfil the long-term decarbonisation agendas of governments worldwide, the share of wind in the energy mix needs to grow further. Thus the windpower market itself will grow and, since the intention of the industry is to produce green energy, it is going to need to think hard about sustainability.
Gearboxes and drives
With this in mind, Rematec held the first International Forum on Wind Turbine Remanufacturing at the Rematec show in Amsterdam in June. The event was at the vanguard of a new trend: the first edition of WindEurope’s End-of-Life Issues and Strategies (EoLIS) seminar was held recently at Leuven in Belgium. What to do with wind turbines is a subject now occupying minds across business and academia.
Wind energy companies set great store by operations and maintenance (O&M). Research by Wood Mackenzie suggests that 205,000 new units will be added to the global onshore fleet by 2027, equivalent to 580GW of capacity. Asia-Pacific, driven by China, will become the largest O&M market in the world in the next decade, the consultancy predicts. “Yet existing fleets in US, Germany, Spain, and Brazil still represent a sizeable chunk of the O&M market,” it says in Global Onshore Wind O&M Trends 2019. “As these fleets age, more focus is given to keeping turbines operating for longer, in the form of lifetime extension activity and reliability improvements.”
The good news is that wind turbines are not dumped into landfill at the end of their working lives – and theyconsist of many components that automotive remanufacturers would find familiar, such as gearboxes and drives. There are clear reman possibilities here: indeed, most of the components in the nacelle – the housing which contains elements such as the turbine’s hydraulics, gears, generators, main bearings and pitch mechanisms – would be up for grabs. “Other major components for recycle include transformers, controls, electrical switching and protection equipment,” explains Bob Sherwin, managing partner for EAPC Wind Energy Services, North America’s sales agent for wind farm software package windPRO. “The electrical industry already does this.”
While some units are rebuilt and installed in other locations, Sherwin says that the most problematic components to deal with are the composite blades and towers, although composites can be ground for other uses, such as aggregates-mixing in roads.
Reman potential
Beurskens believes there is great potential. “A real gap in making wind energy fully circular is re-using rotating parts - bearings for blade pitching, bearings for yawing, gearboxes - and reuse of precious metals from sensors,” he says. “And it is exactly here where reman comes in.”
Philipp Schmid, group strategic marketing manager at SKF, agrees that there is room for reman: “Absolutely! Bearings and lubrication systems are an excellent example to contribute to the circular economy and green energy production.”
Leo Schot, ex-CEO of LM Wind Power, says that original equipment manufacturers (OEMs) are already hard at work on finding end-of-life solutions, such as reusing the material in turbine blades. “I know that LM Windpower is working actively on sustainability,” he adds.
Remanufacturing is required to close the loop and get more circularity, insists Eric Pieterse, business developer at Arkom Windpower. “There is a real good opportunity for the industry to introduce reman in the sector and develop a new business,” Beurskens continues. “The question is whether new companies will jump (or whether) OEMs will include that service into their portfolio. Both options have their specific advantages.” While a lot of components and assets are remanufactured today in wind turbines, Hannes Leopoldseder, business unit manager at SKF, explains that companies may not call it that. “The term ‘remanufacturing’ is not that widely used in the wind industry yet – ‘serviced’, ‘reconditioned’ are the terms often used. Nevertheless it is already done.”
Help needed
Although there is undoubtedly interest, Pieterse sees that more help is needed. “The focus is on growth, and gaining and keeping market share,” he says. “Therefore, I think companies put resourcing on creating and capturing value, instead of closing the product loop. Nevertheless, when there are incentives - maybe induced by governments - same as with electronics, it could stimulate remanufacturing. At least the waste should be centrally tracked, so in case new technologies arise, the supply can be easily identified.”
Wind turbine reman can take heart from the example of car OEMs, which have been remanufacturing their own products for decades in some cases. “The wind energy sector can learn a lot from the automotive sector,” says Beurskens. “Not so much on technical issues, but on standardised processes, logistics and standards.” Certification and standardisation are both vital for reman in the wind energy sector, he insists. Sherwin agrees with this, particularly from the point of view of finance and insurance.
Leopoldseder highlights the fact that the windpower industry is tightly regulated, and suggests: “The certification bodies need to look into the area of remanufacturing more intensively.”
Standardisation in the remanufacturing process would obviously mean that equipment which has been remanufactured should have the same quality as ‘new’ parts. Clients will hesitate to accept a reman part even when the price is reduced – this will all be sounding familiar to Rematec News readers.
But Sherwin and others point out that, while there are things to take from automotive, “the volumes are smaller and the components much larger”.
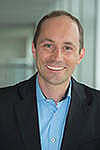
Philipp Schmid, SKF
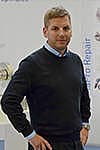
Hanes Leopolseder, SKF
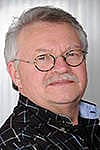
Jos Beurskens, SET
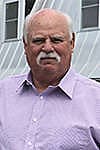
Bob Sherwin, EAPC
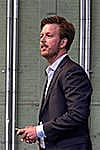
Eric Pieterse, Arkon
Overcoming resistance
“Cars are far more available than wind turbines, so I suppose the market is small,” acknowledges Pieterse. It is a good point. For Leopoldseder, it is worth looking at it more broadly. “We are taking the learnings from other industries like automotive, railway and metals,” he says. “What is impressive in automotive is that remanufacturing is industrialised - and for sure there are a lot of learnings
which can be translated into wind.”
Resistance from consumers is a common problem for remanufacturing but Pieterse says that the lack of availability of sufficient information, parts, data, insurance and so on contributes to this. For Beurskens, it is also a matter of priorities: “I would say that there is no resistance but a lack of urgency - yet - and lack of knowledge from other sectors.”
Bearing remanufacturing is not that well known to the wind industry yet, adds Leopoldseder. “When it comes to quality, we at SKF remanufacture bearings for trains since many years. Railway applications are high demanding applications when it comes to safety as well as performance. If remanufacturing of bearings work in railways, why shouldn’t it work in wind as well?”
Schot is not sure if there is resistance to reman as such and describes common warranty and service arrangements, after which operators can decide to do repair,overhaul and maintenance with someone other than the original supplier. “As wind turbine products increase in size and efficiency while reducing in cost, replacement for a new turbine might be feasible instead of repair. Midlife
upgrades, repowering (other blades) can be options to increase output.” OEMs are interested in new ways of doing things and – in a comment that will chime withanyone in automotive reman – he says: “OEMs show a tendency to organise more control on the service market.”
Resource efficiency
The sorts of resource issues that governments and climate change protesters around the world are currently grappling with are well known to the wind energy sector. How can we manage older turbines effectively – and improve the sector’s resource efficiency?
“The average energy density of the wind - and solar radiation - is quite low,” explains Beurskens. “In order to generate significant amounts of energy for our society, large rotor-swept areas are needed, thus a large number of installations. This means that wind energy technology is a material-intensive energy generation technology. Efficient use of materials is a must to make the technology fully circular.” This is why, he insists: “For each key component (blades, tower, rotating parts, etc), dedicated and well organised reuse strategies need to be - and are being - developed.”
As things stand, turbines can already operate for a quarter of a century. “However, by standardisation, economy of scale and technology development, the costs have been reduced extremely,” Schot says. “Repowering and upgrades are [already] offered or thought of for life extensions and industry is working on solutions to reuse the components, such as blades.”
The market will, in effect, make some of these decisions, suggests Eric Pieterse of Arkom. “It is determined by the business case and finally the project contracts. When clients ask for longer project duration, manufacturers can supply more robust wind turbines with an extended maintenance/turnaround schedule. Somehow an extended wind turbine life should be taken into account in the business case, maybe even before the project is on the drawing board.”
The fact remains that reman is going to have a role to play in wind energy – since it will be good both for the environment, and for companies’ bottom lines. “We have to move from a linear economy to a circular one also for the old turbines still operating,” concludes Schmid from SKF. “Continuing running older turbines can still be a lucrative business. If you use remanufactured bearings you can save up to 50% compared to buying a new one. This impacts the business case in a positive way.”
Share your remanufacturing stories with us
Do you have an innovation, research results or an other interesting topic you would like to share with the remanufacturing industry? The Rematec website and social media channels are a great platform to showcase your stories!
Please contact our Brand Marketing Manager.
Are you an Rematec exhibitor?
Make sure you add your latest press releases to your Company Profile in the Exhibitor Portal for free exposure.