Why are OEMs so careful about sharing their reman technology?
The reluctance of Original Equipment Manufacturers (OEMs) to openly discuss their remanufacturing activities or share information about their remanufacturing technology can be attributed to several reasons. It is not uncommon for OEMs to handle remanufacturing processes internally, rather than outsourcing them to third-party remanufacturers. By keeping remanufacturing in-house, OEMs can have better control over quality, consistency, and intellectual property protection.
OEMs consider their remanufacturing capabilities and processes to be a strategic advantage over their competitors. They invest significant time, effort, and resources in developing and refining these processes to ensure quality and cost-effectiveness. By keeping this information confidential, they can maintain a competitive edge in the market. Remanufacturing technology often involves proprietary knowledge, trade secrets, and patented processes. Sharing detailed information about these technologies could expose OEMs to the risk of intellectual property theft or unauthorized replication by competitors. Therefore, they prefer to keep their remanufacturing practices under wraps to safeguard their valuable intellectual property. OEMs may be concerned about the potential impact on their brand perception if customers become aware of remanufactured products. Some customers may have reservations about using remanufactured items, perceiving them as inferior or less reliable compared to new products.
Remanufactured or genuine parts? That is the question!
OEMs may fear that openly discussing their remanufacturing activities could inadvertently tarnish their brand image. OEMs often position themselves as providers of new, innovative products. They want customers to associate their brand with the latest technology and cutting-edge solutions. Openly acknowledging remanufacturing practices could conflict with this positioning and create confusion among consumers who primarily associate the OEM with new products. Remanufacturing requires a well-managed supply chain to collect used products, disassemble them, refurbish components, and reassemble them into remanufactured products. OEMs may prefer to keep their supply chain networks and partnerships confidential to ensure a steady supply of used products and maintain control over the remanufacturing process. Finally, even if OEMs may be hesitant to openly discuss their remanufacturing activities, they often engage in remanufacturing internally to reduce costs, improve sustainability, and meet certain regulatory requirements. Remanufacturing allows them to extend the life cycle of their products, reduce waste, and offer more affordable options to customers.
The OEMs are known for their in-house remanufacturing capabilities
These are just a few examples, and other OEMs across different industries may have in-house remanufacturing capabilities. It's important to note that the extent of their in-house remanufacturing operations and the specific products they remanufacture can vary.
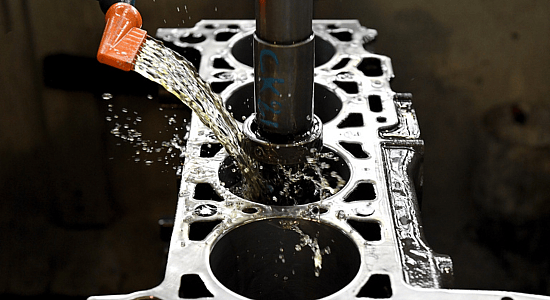
Original Reman arises in the certified FPT Industrial (Iveco Group) plant as the result of a very comprehensive industrial remanufacturing process. It means regenerating components to make them perform as well as new parts, guaranteeing such a level of quality in line with the latest Original Equipment specifications. FPT Industrial/Original Reman always adopts the most advanced technologies, as the new cleaning machine does not require human assistance and allows it to speed up the process while improving accuracy.
Ford Motor Company has a remanufacturing program called Ford Remanufactured Parts. They remanufacture various components, including engines, transmissions, alternators, and starters for their vehicles.
While Bosch is primarily known as a supplier of automotive parts, they also engage in in-house remanufacturing. Bosch Remanufacturing Services focuses on remanufacturing automotive components, such as starters, alternators, diesel injection systems, and electronic components.
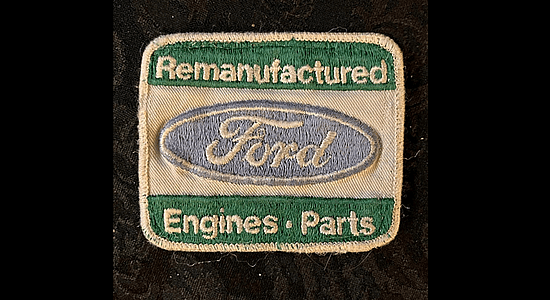
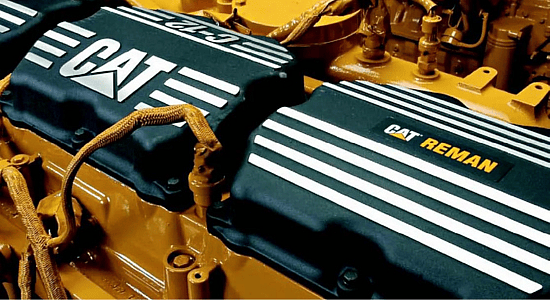
Caterpillar, a leading construction, and mining equipment manufacturer, has a dedicated division called "Remanufacturing & Components Division" that focuses on remanufacturing various components and parts for their machinery. Cat remanufactured parts and components provide same-as-new performance and reliability at fraction-of-new costs—while reducing the impact on the environment. And over-the-counter availability gives customers more options at repair and overhaul time. The results are maximum productivity and lower costs.
Share your remanufacturing stories with us
Do you have an innovation, research results or an other interesting topic you would like to share with the remanufacturing industry? The Rematec website and social media channels are a great platform to showcase your stories!
Please contact our Brand Marketing Manager.
Are you an Rematec exhibitor?
Make sure you add your latest press releases to your Company Profile in the Exhibitor Portal for free exposure.